Vietnam’s auto part makers drive forward but hit potholes
(VEN) - Vietnamese part manufacturers for the domestic auto industry have been increasing their market share in recent years and face a promising future with the growth of domestic demand for cars, but their progress is being hampered by import pressures.
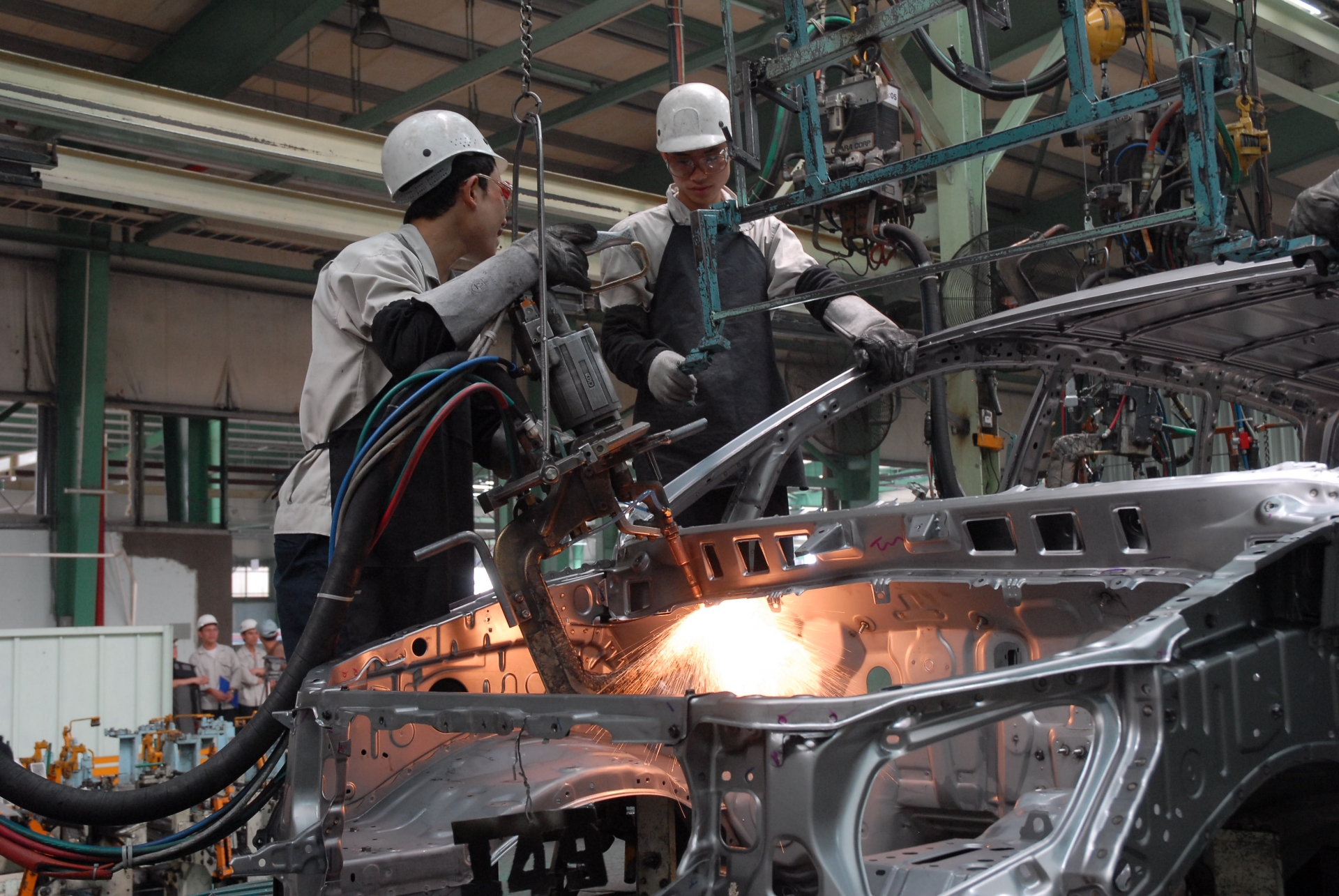
Positive outlook
While most Vietnamese manufacturers produce only small components and spare parts for the auto industry, an increasing number of them are now capable of manufacturing molds of all kinds, bicycle and motorbike components, standard mechanical components, power cables, technical plastic and rubber components, tires and tubes of all kinds. A number of these products meet much of the domestic demand and are exported as well.
For example, three years ago, the Southern Rubber Industry Joint Stock Company (Casumina) began producing passenger car and light truck tires meeting the demanding standards of the US market. In 2020, the company launched its own tire brands for size A and B passenger cars.
In 2020, a ground-breaking ceremony was held for the Thanh Cong Viet Hung automotive supporting industry complex in Ha Long City, Quang Ninh Province, which will house many automotive supporting industry firms, especially high-technology ones.
The Hanoi Plastics Joint Stock Company (NHH) is another typical example. This enterprise produces and supplies more than 40 percent of plastic components for Honda and other multinational companies operating in Vietnam. Thanks to continuous innovation and improvement, NHH has become a reliable partner of Honda, Toyota, Piaggio, VMEP, Panasonic, LG, VinFast, Visteon, and Hyundai. NHH and Toyota have reached the level of self-designing, manufacturing plastic molds and processing automotive plastic detailed inspection kits. In 2019, NHH cooperated with VinFast and supplied more than 50 percent of the plastic parts for VinFast's electric motorcycles.
Removing bottlenecks
In its development orientation, Vietnam's automobile industry is considered an important driving force to promote the industrialization and modernization of the country, with its products serving both domestic and export demand.
However, the Vietnamese automobile industry faces stiff competition from nearby countries and still has to import 80-90 percent of all raw materials required to produce cars, making cars 10-20 percent more expensive than imported ones.
The Ministry of Industry and Trade has suggested focusing on easing two bottlenecks in market capacity and cost differences compared with other countries in the region. The top priority is to protect the domestic market through technical barriers in accordance with international commitments, and encourage trade exchanges between regions in order to promote automobile consumption.
From a manufacturer's perspective, Nguyen Trung Hieu, Head of the policy subcommittee of the Vietnam Automobile Manufacturers Association, said development of the supporting industry for domestic automobile manufacturers is hampered by the small market size, lack of raw materials and low technical level. Additional state support is needed to overcome these weaknesses, keep up with other countries, and reduce gaps in production costs through tax rate support.
Given the increasing pressure from imported cars, many companies are also urging preferential policies on component imports.
The Vietnamese automobile market is forecast to reach nearly one million units by 2025, offering growth opportunities for the automobile industry. If Vietnamese enterprises and policy-makers do not make good use of this opportunity, Vietnam's auto-supporting industry will continue to lag behind other countries in the region and domestic enterprises will act mostly as assemblers or small-scale manufacturers.